Shopping Cart payment system issues:
If your card is getting rejected it likely is the security on your card provided by your bank. Often times your bank will text you or call you to verify it is actually you making the purchase. Sometimes it is the merchant processor. This is because my original merchant account was for my last business (Fern River Resort). There is left over code from my past merchant account somewhere in Google or other location that nobody can find to correct.
Certain banks see this and call an error thus blocking the transaction. The fix is: Use a different card or call your bank. Your bank will than approve the charge. Sorry, this is the new world where everyone is trying to stop scammers.

Servo Motor User Manual (Replacement board)
This page will not work on your smart phone. Use a PC!
These instructions are for 2023 year model and earlier controllers.
They do not apply to 2024 or 2025 year model controllers.
Sorry but I am too busy building motors to write the 2024 and 2025 programing
pages at this time.
P 17 must be programed first and correctly. If not programed correctly your motor and or main board could be damaged beyond
repair. Additionally serious body injury even death is possible due to the servo motor running so fast that it explodes.
All images and information found on this page is copyright protected.
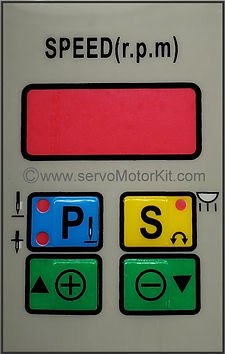
1: 750W with 4,000 rpm limit
2: 8-pole 550W motor (see 6 pole below)
3: 6-pole 82mm diameter 400W motor.
4: 600W & 800W motor.
5: Unknown
6: Our 1,000W & 1,500W motors.
To set/program control board:
A. Press both & at the same time for 1 second to enter programing mode.
B. Use or Scroll up or down to
C. Click to enter select correct P-__ setting for motor. See list below.
D. Use or Scroll up or down to the correct P -__ is displayed, See Below
Choose Motor type:








7. Unknown
8. Our 6-pole 550W motor + 500W 76mm
9. Our 6-pole high performance 750W
Includes 650W 76mm motor.
10. Unknown. 11. To be announced.
12. Our High torque 6-pole 900W 76mm
motor.
E. With correct motor number in the display: Click to save the p-17 parameter for your motor.
The control unit will flash IN while loading your motors settings, reset and display:
Now you are ready to program upper and lower RPM limits as well as braking and soft start. See below.



With P-17 set correctly as seen above
To change forward reverse motor direction
F. Display will show Hold down For 3 seconds until display shows Release




The red dot in lower right corner of display indicates motor direction. Reversed with light on. Also motor must be stopped with power on to reverse direction.

G. Set low RPM stop:
Press both & at the same time to enter programing mode.
Use Scroll to Click to enter rpm's. Scroll to the bottom limit of choice. I choose
Click Display will return to This is ready to run.
# Consider This when setting speed below 1,000 RPM's:
It would appear that there is a power level adjustment function. Setting the low speed to 300 produces less
torque than setting it to 380 but the motor still runs at 300 rpm's.








The Manufacturer recommends no lower than 500. Some will program as low as 100 rpm. This is problematic as it can cause motor to drop out. If that happens, increase bottom rpm limit. Also consider a lower gear ratio so that the motor can run faster while the spindle runs slower.

H. Set high RPM stop:
Press both & at the same time to enter programing mode.
Use Scroll to Click to enter rpm's. Scroll to the top limit of choice. I choose
Click Display will return to This is ready to run.








The Manufacturer recommends no higher than 4,000. I always set to 4,500 except: Check top speed the motor will run. If it only reaches 3,900 than program the high stop to 4,000. This will actually improve the motors top speed about 50 rpm and no more. Setting a motor that tops out more than 100 above top speed will actually reduce performance.

I. Set soft start / Acceleration speed:
Press both & at the same time to enter programing mode.
Use Scroll to .P - 06. Click to enter. Choose between . 1. ~ . 9. I choose . 1.
Click Display will return to This is ready to run.






Soft Start and acceleration speed are one and the same.
Set to 1 is beneficial as it saves the belt and motor from sudden acceleration (0 to 4,500 rpm in seconds).
Higher numbers allow the motor to maintain a constant speed during load changes. My big lathe runs best set at 3 or 4. You will have to find what is best for you.

J. Set Braking:
Press both & at the same time to enter programing mode.
Use Scroll to .P - 08. Click to enter. Choose between . 0. ~ . 5. I choose . 0.
Click Display will return to This is ready to run.






Braking speed is the opposite of acceleration speed.
Zero is soft on the belt and almost allows the machine to coast to a stop.
Higher numbers allow the motor to to rapidly stop the lathe. This is beneficial for thread cutting as it allows for stopping on a dime. You will have to find what is best for you.

You are now ready to run your machine.
Below I will list the rest of the Parameter #'s but you should not change them.
I will also go into the diagnostics and problem solving.

Accessories:
1. LCD Light: Momentary push the The red dot in the yellow S button will light up Or turn off.
While on there are 5 clicks that increase brightness
2. External hall effect position sensors. This is not installed. If you hold It will light the lower LED Push it again
and the other light is on. You just commanded the motor to stop at a non existent hall effect sensor. You now must hold down
the blue button for four seconds until the LED turns off. If you run the motor with either light on you will get a fault code 5.
E5 . In order to fix E5 . Turn off the control unit and wait for it to power down.
Turn control unit back on. With in the display hold down Until both lights are off like this: Now you
can run the motor again without a fault code.
See diagnostics and fault codes below if this does not work.








By now you should know how to access all parameters so I will describe the rest fast and short
You should not need to change any of them anyway.
.P - 03. Set to 0. Stop position for external sensors as described above in accessories. Requires extra sensors not included. 0 = down 1 = up
.P - 04. Set to oFF. Do not open unless external sensors described above are installed.
.P - 05. On or off this just changes if the red reverse light indicates on or off in relation to the direction of the motor.
.P - 06. Soft Start and acceleration speed are one and the same. See initial set up procedure above (light green background).
.P - 07. Brightness pf LED light. See accessories above.
.P - 08. Motor braking. See initial set up above.
.P - 09. set to oFF. Position adjustment. Not used without additional sensors.
.P - 10. set to . 10. Position adjustment. Not used without additional sensors.
.P - 11. set to oFF. Speed Lock function
.P - 12. set to . 50. Action time between external sensors/
.P - 13. set to 1. Synchronizer type.
.P - 14. set to 1. Not used.
.P - 15. set to 1. Speed display on. Note no other setting accept off is available.
.P - 16. set to oFF. Factory reset.
.P - 17. See top of page. This is where you you select the motor and it is the first step. Any changes will reset everything to a new motor size and default settings.
.P - 18. . 42. Software version 42 is best for 2023 and earlier. 43 is required for reverse on the fly
.P - 19. set to oFF. High speed Kp coefficient PID regulator. Off is default. On does nothing so far.
.P - 20. set to 0. 0 is default. The higher P-20 is set the longer initial acceleration is delayed.
.P - 21. set to 400. No use.
.P - 22. This is system speed limitation. Use .P - 02. to limit top speed.
.P - 23. set to 1. Motor strength 1~3
.P - 24. No use.
.P - 25. set to . 10. Low speed Kp coefficient PID regulator.
Notes:
1. Noisy likely means P-17 is set wrong and it's firing the fields at the wrong time.
2. Many motors have a physical limit as to how fast or how slow they will run: Programing them to run faster or slower than the physical
limit will actually reduce top speed and performance. For this reason: If your motor tops out at say 3,900 RPM, set the top speed at no
higher than 4,000 RPM, This will actually improve top speed by as much as 50 RPM's
Fault Codes
Check this first:
If you have a fault code ER 5 it is most likely incorrect hall effect sensor settings.
See white background Accessories section above, line 2.
Next check P- 4 make sure it's set to off.
__________________________________________________________________________________________
ER 1 Over voltage
Check input power voltage or replace main board. Usually resulting from a jam or shorting out speed switch.
ER 2 No Information
- - - - - - - -
ER 3 Over current
Check motor connector, or replace main board. Usually resulting from a jam or shorting out speed switch.
ER-3 is almost always a burnt mosfet. See how to test it and replace it, click here to watch 0ur YouTube Video
Buy mosfets here: OEM mosfets
ER 4 Rotary switch fault
Check switch position. Usually the speed switch is unplugged. See below diagnostics. Contact me if in warranty.
We have replacement switches, please contact us to make sure you get the right one:
ER 5 Synchronizer fault
Check Synchronizer connector and position signal. Our motors are not equipped with external synchronizer. See below.
ER 6 Hall fault
Check motor connector, or replace motor. See below.
ER 7 Lock rotor fault
This is usually caused by binding and jamming. not in motor but in your machine. Check motor connector, or machine head.
PD Speed Switch
Turn speed to zero and wait 5 seconds. Cycle power if required. Possible defective speed switch.
Diagnostics V. Check speed switch and Motor Function:
The below info is not for the inexperienced.
To enter readout function:
Press and hold down Turn power rocker switch on.
As soon as you hear a click, release the yellow button.
Your display should look something like this:
That is the speed switch # A in stop position.
Press to switch between A, B & C below.
# A Speed control switch:
Rotate from stop to run, displays: L2.68 or close to it.
Rotate from run through full, displays: L2.68 ~ 84.09 or close to it.
Voltage is what is shown on the last 3 digits. Ignore the first symbol.
B. Synchronizer not equipped, this is an external component.
Display will show:
Turn the wheel:
“U” will be displayed to show position 1
“D” will be displayed to show position 2
C. Hall Sensors in Motor. (Fault Code 6)
Rotate motor to display hall value:
Display will read C 1 through C 6 as you rotate by hand.
Fault state, If you get an “E” in any position:
That hall sensor is defective. The general thought here is
the motor needs to be replaced?
We have hall sensors.
This job is very difficult to perform successfully. That is why most just say replace the motor.
However if recent events have you wanting to fix it for as little as possible. See links below:
550W, 750W and 900W use these: Hall sensor set small motor
1,500W These should be easier: Hall sensor set 1500W motor










